The TTLM I/O load module is designed for critical force measurement applications where accuracy, extreme stability, and dependable noise rejection is essential
The signal conditioner is a load measurement device and is used as an analog output (+/- 10 VDC), from a peak hold circuit, to be used with such PLC families as Allen-Bradley & Siemens as well as other data acquisition systems. These systems will provide the display and alarm control functions.
The TTLM has high sensitivity levels that work well in an electrically "noisy" environment. It has two amplifier gain ranges (span ranges) and can accept either weak or strong signals from the load sensor.
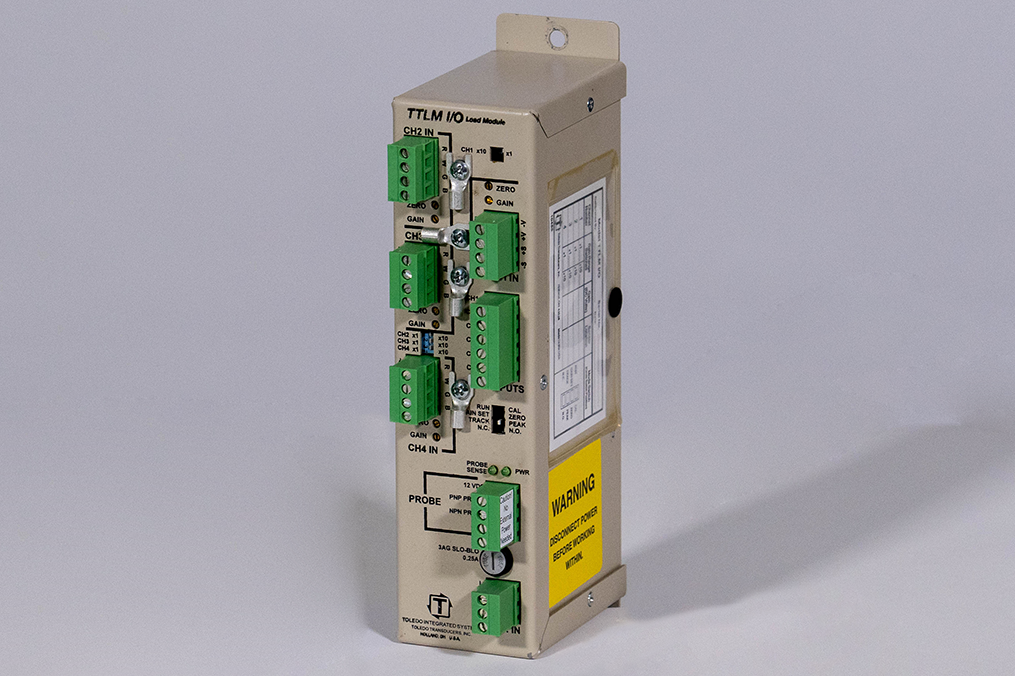
The TTLM module is available either in an AC version [customer selectable between 110V and 220V] or a 24 VDC version, depending on the power source the customer wishes to use. The 24 VDC version is certified to be in conformance with European CE standards. Either version is available in one, two or four channels.
The TTLM is included in our tonnage kits. These kits include the TTLM (signal conditioner), PM Kits (strain gauge sensors) and the ladder logic and screen programming needed to include tonnage monitoring into your existing PLC logic.
Standard | Option | |
Signal conditioning module for strain gauge sensors & load cells |
✓ | |
Four independent channels for accommodating up to eight sensors |
✓ | |
Uses full-bridge sensors from 120 Ohms to 1,000 Ohms |
✓ | |
Plug-in connectors are used for the sensor inputs |
✓ | |
High/low sensitivity span ranges selected with front panel switch |
✓ | |
Power input/output are plug-in connectors |
✓ | |
Built-in automatic peak load memory circuits |
✓ | |
Peak measurements are made with an external trigger device |
✓ | |
Built-in power supply for stable operation and noise rejection |
✓ | |
Compact size to fit almost any location | ✓ | |
Steel enclosure for maximum protection and noise rejection |
✓ | |
Automatic Zero Balance | ✓ | |
From one to eight sensor inputs, one or two per channel |
✓ | |
Analog output terminals | ✓ | |
CE Certified | ✓ | |
PLC Ladder Logic | ✓ | |
HMI Screen Program | ✓ |
No. Of Channels | One, Two, Three or Four |
Sensor Inputs | Full bridge strain gauge sensors 120 to 1000 ohms Up to (4) 350 ohm sensors |
Sensor Excitation | Built-in 12VDC @ 300mA max (Short circuit protected) |
Sensor Input Connections |
4-pin .2" pitch Phoenix connector |
Auto-Zero Time Constant |
10 seconds |
Balance Range | +/- 1mV/V of offset |
Gain Range | Low Gain = 100-1,000x High Gain = 1,000-11,000x |
Analog Output | +/- 9VDC |
Analog Output Connection |
6-pin .2" pitch Phoenix connector |
Peak Decay | Less than 1% of full scale in 10 minutes |
Accuracy | +/- 1% of full scale max |
Non-linearity | +/- .1% of full scale max |
Frequency Response |
Flat DC to 1KHz |
Resolution | Not Applicable |
SPM | 2000 SPM (probe trigger for peak capture) |
Calibration Shunts | 1 Meg Ohm .1% precision resistor |
Computer Interface |
No |
Trigger | Probe for peak capture |
Threshold Probe | Built-in voltage source (12VDC @ 50mA max) provides power for NPN or PNP proximity probes. Also supports limit switch, solid state or mechanical relays |
Resolver Interface | No |
Shutdown Relay | No |
Power Req. | 12 Watts max, 100-130VAC @ 50-60Hz OR 200-260VAC @ 50-60Hz (Use 5mm x 20mm SLO-BLO fuse) |
Expansion | No |
Operating Temp. | 0-70 degrees Celsius |
Weight | Approximately 4.0lbs |
Width | Height | Depth | |
Dimensions | 2.25 " | 9.00 " | 4.00 " |