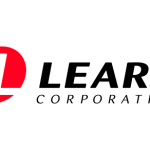
Stamping at Lear Proves that Data Rules
October 10, 2024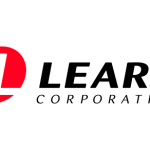
Stamping at Lear Proves that Data Rules
October 10, 2024Monitoring press automation control function systems can direct operators to sources of trouble.
By Daniel Falcone
In the past, it was not unusual for a metal stamper to equip a press with one control box for die protection, another for tonnage monitoring, and others for programmable limit switch functions, lubrication system controls, feed controls, shut height monitoring, and other automation control functions.
When a fault occurred, an operator had to start looking. Was the problem in the die or the press? Monitors mounted in a variety of locations on the press had to be checked, and because of limited space, boxes were often mounted in less-than ideal locations. The operator had to deter mine which box indicated a fault, fix the problem, go back to the box to reset the control, and then return to the operator station to start the press.
These monitors help reduce the frequency of press and die crashes, and the ability to set dies to known tonnages or designated shut heights can help reduce setup times and their associated costs. However, separate training may be re quired to operate each stand-alone monitor, and if monitors are purchased from different suppliers, entirely different operating routines might have to be learned.
Eliminating Guesswork
Today, monitoring and control equipment can be tailored to different applications. For manually fed presses, stand alone monitors may provide all the protection required because an operator removes a part and places another piece of material in the press before he makes another hit. In manual applications, monitoring part ejection may not be necessary, but monitoring tonnage may still be important, especially during the die setting.
An automatic press, however, may be equipped with a multi-station progressive die that has many functions that should be monitored to ensure proper operation. When a coil feeder is used, part lubrication and many other tasks must occur during each press cycle, or disaster can strike. In addition to the costs associated with lost production, a die crash can be costly to repair.
Setting up dies to known tonnages removes guesswork and experimentation from the process. Tonnage monitors are like speedometers in that they provide specific readings; without them, die setters must estimate how much tonnage they are using.
The monitors allow operators to use the least amount of tonnage possible to produce good parts, which saves wear and tear on stamping dies and presses. High and low set points can be established, and if tonnage varies outside of these limits, the press will stop.
Shut height monitors provide similar safeguards, allowing a die setter to set up a job to a known shut height to remove the guesswork from the process of setting a ram. Die, protection monitors, provide additional protection while a press is operating by tracking material as it progresses through the machine and shutting down the press if a part fails to eject before a subsequent machine cycle.
The monitors allow operators to use the least amount of tonnage possible to produce good parts, which saves wear and tear on stamping dies and presses.
Levels of Control
Although most stamping plants have both automatic and manual presses on the floor, the machines should not be treated the same.
Automated presses may benefit from a system that combines as much control and monitoring as possible. A programmable logic controller with a single man machine interface (MMJ) display can be installed on a new press or retrofitted to an older model. A variety of MMis are available, many of them personal computer (PC)-based and featuring mono chrome or color displays. Screens can be customized in-house to display information in whatever form a user requires, and touchscreen displays are available.
In addition to die protection and shut height and tonnage monitoring, the following are typically available in control systems:
Programmable limit switches.
Brake time monitoring
Job or recipe storage
Counters
Resolvers
Counterbalance control
Servo feed interface
Preventive maintenance logs
Production data
If a fault occurs during a press run, an MMI automatically displays the function in which a failure has occurred. For ex example, if a sensor detects a buckle in the material, an MMI screen will direct the operator to the fault.
By indicating to an operator where a problem is, the system helps to increase uptime by eliminating much of the effort previously spent identifying the trouble. Time and date stamped alarm and fault histories can be stored automatically by many systems to help track the events.
Networking a programmable logic controller to a central computer can make available production and downtime re ports and preventive maintenance logs. Reports can also be customized to meet a variety of requirements.
Just-in-time (HT) manufacturing also means "almost gone," and frequent die changes are routine in most stamping plants today because inventories are often kept to a minimum. If a variety of jobs are run on the same press, setup time can be reduced by storing machine settings for specific jobs in a programmable controller. Once entered, settings can be re called anytime the same job is run.
A programmable logic controller is also expandable. The controller is designed as an "open" system that can be customized to a stamper's needs. Suppose, for example, that a stamper at first needs only a couple of die protection and limit switch monitoring functions. Later, tonnage monitoring, counterbalance control, and servo feed and shut height monitoring can be included by adding plug-in cards to the controller.
Dual clutch/brake programmable logic controls that meet the requirements of the American National Standards Institute (ANSI), the Occupational Safety and Health Administration (OSHA), and Canadian safety mandates are also available. The dual system uses two programmable controllers to create an actively redundant system. The two controllers must always agree or be in unison, or the press will not operate.
Weighing Needs
How much control and monitoring does a stamper need? Requirements vary, depending on the job being run. When considering a system, a stamper should weigh the monitoring and control needs for the most complicated die that is run on a press. The same press may run several dies that have different monitoring requirements, and the control system should give the user the flexibility required to handle all dies and jobs run on a specific press.
A common pitfall encountered by stampers setting up a new system involves a system's ease of operation. If a system is too complicated, press opera tors will not take advantage of all features available. To counter that potential problem, MMis are available that are intuitive and offer online help screens.
Installations can be handled in several ways. Most stampers can install these types of systems by following instructions from a supplier. Most systems are packaged to allow quick installation, but some stampers look to their suppliers to offer either a turnkey installation or assistance with the process. Most suppliers will work closely with the customer on installation and offer the key to success with a new system.