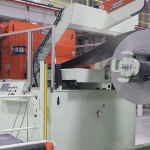
High Coil Feed Line Case Study
October 10, 2024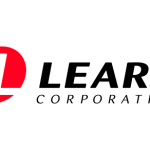
Stamping at Lear Proves that Data Rules
October 10, 2024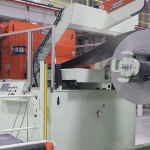
High Coil Feed Line Case Study
October 10, 2024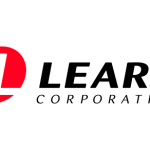
Stamping at Lear Proves that Data Rules
October 10, 2024This manufacturer has significantly increased production for a redesigned version of its largest-selling caster model by integrating stamping and assembly operations under the control's latest available press control technology.
Colson Caster Corp., Jonesboro, AR, offers more than 35,000 different caster models-from tiny chair casters to giant industrial types. For more than 100 years, the company has led in the design and development of new cutting-edge products of caster and wheel technology.
Theirs is a competitive industry. Selling directly to OEMs and through a network of stocking distributors, the company must continually provide improved products and on-time deliveries to succeed.
Concurrent Engineering
When the company decided to upgrade the base unit of its most successful caster model, design and manufacturing teams worked to together to automate, as much as possible, the entire caster production process. The new product has an increased load rating over the previous model, and the cell manufacturing process provides more efficient production with higher quality than the previous method of production.
Colson's recently completed caster manufacturing cell involves stamping, subassembly, plating, and final assembly processes. The cell has enabled the company to significantly increase production while decreasing the number of individuals required to produce the newly re designed caster from 29 to 17.
According to Byron Glanton, manufacturing engineer for Colson Caster, "Our older manufacturing method required that blanks be stamped, washed, and delivered to our production presses for stamping. Axle holes had to be pierced before forming the part, which at times led to alignment problems during assembly."
By redesigning the caster and the manufacturing method concurrently, we were able to bring the blanking dies into our rebuilt 440-ton Aida transfer press. This eliminated separate blanking and washing production steps. Now we can blank, transfer blanks into the draw die, form the part, and pierce axle holes after the form, all in one operation."
After the forming process, the stamped part is transferred automatically to the subassembly and plating processes. The resulting part is known as a "generic assembly," and is the base for the next generation of Colson's most popular caster style. The subassembly comes off the line completely.
The final assembly process involves installing mounting options, automatic greasing, and quality checks, and finally installing the proper wheel. Production of the current model, which the new caster will replace, is approximately 1,500,000 units per year. Estimates for the new model run up to 2,000,000 units per year.
New Production Moving Forward
Production control is Key
According to Glanton, when the Aida press was purchased in February of 1996, the controls and transfer system were both out of date. "We had to update the press controls, already we knew that we wanted to drive the production system using Allen-Bradley PLCs.
Through the quoting process, a press control system offered by Toledo Transducers covered all areas we wanted to address, including die protection, press protection, tonnage monitors, and press counter balance control.
"The service we have received has been wonderful. If there is a problem, they can dial up our press control and diagnose the problem online."
One big advantage of the press control system noted by Glanton is a significant decrease in the time it takes to train an operator. Every thing the operator is expected to do can be read right off the control console. Additionally, a servo interface controls the feeder so that when a new tool is installed, a bimuy-wiring unit is plugged into the blanking die, which updates the system. It reads the tool number, relays the information to the press control and automatically updates all press parameters, including counterbalance control, speed, feed, etc."
We believe this is the first installation of its type in the caster industry. Moreover, as we get up and running, we see other opportunities to further automate the process. One is by using an automatic vibratory bowl feeder instead of an operator between the plating line and final assembly operation to load a generic fork assembly to the base unit.
"One of the biggest areas of improvement comes in the final assembly area during the installation of the wheel. It formerly took three people to do 225 wheels/hr. Now we can assemble 750 wheels/hr., in an auto mated operation."
The subassembly, tied to the speed of the press, is produced at a rate of about 2400 pieces/hr. Four finished fork assemblies are fed to subassemblies at the same time, resulting in a total production of 2400 pieces/hr.
According to Glanton, "This new caster product, which we call a Four in-Four. is much anticipated. It is more decorative than a welded type and has an industrial load rating. It was redesigned to be manufacturing friendly and will allow us to get more variations of our base unit to market quicker and at a lower cost than our competition.
"Designing this product using concurrent engineering principles has given us the ability to combine form, function, strength, and manufacturability in the best possible unit. We are excited about its potential in several markets, including food ser vice, shopping carts, and various industrial and institutional applications, depending upon the wheel option selected.”