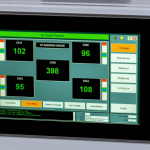
The Importance of Tonnage Monitoring
October 10, 2024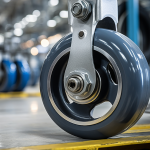
Metalforming 1998 Universal Story
October 10, 2024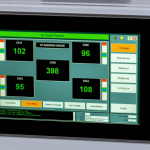
The Importance of Tonnage Monitoring
October 10, 2024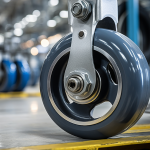
Metalforming 1998 Universal Story
October 10, 202472" Aluminum Alloy Coil Feed Line Case Study -Toledo Integrated Systems
Toledo Integrated Systems Toledo Transducers
The automotive industry demands innovations every day to stay on the cutting edge of technology. When this feed manufacturer was tasked with developing a coil feed line capable of straightening and feeding a high-strength aluminum alloy into a 1200-ton servo press at a Tier-1 automotive supplier- Toledo Integrated Systems was contacted.
TIS was to design, build, program, and commission the Allen Bradley control system for the new coil feed line. Engineers at TIS worked with the team from the feed manufacturer to develop a control system that could meet the requirements of the new feed line.
72" Coil Feed Line
Control System Key Features:
Allen Bradley Compact Logix processor
Two-hundred job recipe/ storage
AB Powerflex 755 drives
Cam-based feed initiated from press control
Two AB PanelView Plus touchscreen HMI displays
Feeder servo motor and drive diagnostics on HMI
Individual E-Stop diagnostics
Ethernet communications
Control and monitoring of all motors used within the feed line
Automatic alarm messaging and fault history
Automatic coil centering on the mandrel
Automatic drag brake adjustment
Method:
All the control panels and enclosures were designed and built by TIS. Wiring and components were inspected and then shipped. Once at the feed manufacturer, the control was installed and wired to the feed line. After the installation was complete, an engineer from TIS commissioned the feed line. The next step was to verify all emergency stop and safety circuits were properly working. A check of all 1/O was conducted along with Ethernet communications. All drives were calibrated and tested. All motors were tested and checked for proper rotational direction.
Finally, all lasers were calibrated and tested.
Coil Load Station
The feed line was then shipped to the end customer, where it was installed. The TIS engineer continued commissioning the feed line control on site. The interlocks and safety circuits for the press and feed line were tested. All motors and drives were checked and tested again along with all 1/0. All calibrations and Ethernet communications were checked and tested.
The feed line was then ready to be tested with the material. The TIS engineer worked with members of the feed manufacturer and the end customer to load the first coil of high-strength aluminum alloy onto the mandrel, threading it through the feed line. Press operators were trained by the TIS engineer to ensure proper procedures were being followed.
On-Site Upgrade:
Feed Line Main Operator Console
During the final commissioning for the coil feed line, a situation occurred where the material being moved by the transfer system met the material to be fed next to the die. The TIS engineer then modified the PLC program to move the material back a specified distance- after the part was cut and before the transfer began to move the material.
Results:
The finished project was a success. TIS was able to incorporate all the necessary features for the feed line control as well as the added features desired by the customer. With communication to the press control and the ability to store up to two hundred job recipes, setup times were reduced. With touch screen HMLs that were easy to navigate and included important line diagnostics; operators were more efficient which also reduced downtime and setup time.