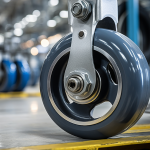
Metalforming 1998 Universal Story
October 10, 2024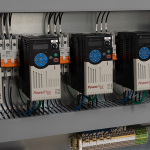
Monitoring Press
October 10, 2024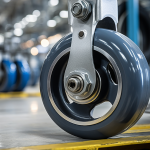
Metalforming 1998 Universal Story
October 10, 2024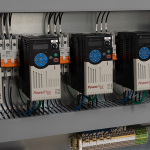
Monitoring Press
October 10, 2024With networked PCs on every press, the Lear plant in Roscommon, MI, enjoys the benefits of live production data and uses that information for downtime analysis, die-set reporting, and more. Productivity has soared as a result.
Since it installed touch screen personal- computer-based controllers on its presses, in conjunction with PLCs for monitoring and controlling ancillary press functions, the Lear Corp stamping plant in Roscommon, MI, boasts almost Herculean improvements in process efficiency and productivity. The plant, with 12 presses that help it ship 1 million parts per week, improved its pressroom output by 65 percent over a nine-month-period and brought die-change times down from an average of two-plus hours to 44 minutes, all while reducing its standard run quantities from an average of 5.1 weeks down to less than five days.
Plant engineering manager, Tim Bossingham, explains the productivity push:
"With networked PCs at every press for live production-data gathering, management now can take snapshots of the pressroom, perform downtime analyses, and view die-set reports. Before, everyone had an opinion of what might be restricted throughout and delaying production. Now we speak with data and take corrective actions before small problems become big problems. If you don't know what's happening out on the floor, you don't know what corrective action to take."
So Much to Learn, So Little Time
When Lear purchased the Roscommon stamping plant from ITT, in 1997, the eight-press facility billed $19 million in sales. Today, it runs 12 presses and will bill $44 million in 2003, supplying three Lear seat track assembly plants with structural-assembly stampings and assemblies for automotive seats, such as seat-frame components, torsion bars, seat-recliner mechanisms, and power seat-track assemblies.
As Lear consolidated operations in recent years, it asked the Roscommon facility to step up and find ways to take on more work. In 2001, to get a handle on its pressroom activities and quantify non-productive shop time such as unscheduled press downtime and pro-longed and repetitive die-set hiccups, Lear invested in new press-automation controllers (Maximizer units from Toledo Integrated Systems, Maumee, OH) for three of its 12 presses.
The Roscommon team's immediate challenge in June 2001: Get those controllers online to gather and analyze data and connect the nine remaining presses. By that August, six presses were connected and sending data upstream to management. By December 2002, all the managers could track activity at all 12 presses—six 400-ton models, a pair of 250-ton presses, and a 200-, 300-, 500- and 800-ton press.
Maximizer press controls offer basic functions such as tonnage monitoring, die protection, die and job storage, counters for parts, batches, die strokes, and bins, as well as options including the display of shut-height adjustment, a servo-feed interface, tonnage-signature analysis, and preventive-maintenance logs. Add Toledo's MaxNet customizable networking software, which allows users to interface presses via a LAN, as has Lear, and management gains compiled databases it can use to create a variety of reports. These include downtime reports, production analyses, shift summaries, and individual operator job output.
The Roscommon plant purchased nine MaxNet licenses so that several people—the operations manager, materials manager, engineering manager, plant manager, tooling engineer, and maintenance engineer—can access the data and run reports simultaneously. They can view live data from every press, view the counters, see the reasons why a press might be down, and which job is loaded, and check the run schedule. They also can collect the data and, perhaps most usable to them so far, compile downtime reports that let them see the most common reasons for downtime. Operators enter this information right at their press control, using custom menus.
Downtime Reporting: Lessons Learned
Every press control includes a card swipe, and all employees have their ID cards that they must swipe every time they perform work on a press.
"We maintain five levels of access— Level 1 operator, Level 2 die setter, Level 3 toolroom, Level 4 maintenance, and Level 5 master," says Bossingham, "When anyone performs work on a press, whether it be die tweaking, shut-height adjustment, etc., we know who did the work, how long it took and why the work was done. Then we extract that data from MaxNet to create downtime reports."
The Roscommon team attributes the downtime-reporting function of MaxNet as the biggest contributor to productivity and efficiency improvements. The downtime reports, which can be run by shift, by individual press, or by operator, let the team quickly identify the leading causes of press downtime and address them.
That's exactly what has been done. The team had, for example, found that operators continuously adjusted the pneumatic shaker conveyors, so they bought new mechanical shakers, and downtime relative to shakers decreased by 50%. Also, presses stayed down while operators waited for hi-lo drivers to deliver material and change part bins. So, the plant purchased stand-behind pallet jacks to replace several hi-los on the floor. Now, the remaining hi-los come by and drop a few bins at each press and take parts away, and the operators use the pallet jacks to change their part bins so presses can continue to run.
Another downtime issue quickly addressed, once identified, was simply too few operators. The Roscommon team discovered that presses sat idle because operators were pulled away to perform ancillary functions or help at other presses. Two years ago, Lear had only 10 operators to run the 12 presses, the theory being that at any one time during a shift, some presses were undergoing die setups and not running production anyway. MaxNet data showed management that it needed more operators, as presses ready to run had no operators to push the button. Management went to Human Resources for help and immediately added several press operators to the ranks.
Die Sets, First-Time Die Yields, and Action Plans
Lear-Roscommon stocks 420 active dies, with an average of 40 under service at any given time. As the shop's standard run quantities have shrunk, a total-productive maintenance scheme has been critical in avoiding emergency die repairs and ensuring efficient last-part-off to first-part-off die changes.
The Roscommon team can run a Die Setter Production Report that gives the total setup time for the day, by shift, or even by the die setter. Managers then can see which dies take the longest to set and take corrective actions to make sure they focus improvement efforts where they will get the biggest return.
Also gathered from that report are data showing first-piece die yield, displaying the number of good parts run on a newly set die before that die needed attention from the press operator or a tool maker. Once they tell MaxNet what minimum number of parts is satisfactory as a good first-piece die yield, the program identifies which dies are causing the most problems.
Bossingham showed us a recent Die Setter Production Report that covered one week of work on all presses. Over that time, the shop set 277 dies, 230 of which met the requirement as a good or acceptable first-piece yield.
"Once we study the report," says Bossingham, "we can write action plans to improve the performance of the dies that continually fail first piece die yield. The report can be exported into an Excel file and sorted to find the repeat offenders. Maybe one die constantly breaks punches, or one might need more lift in one area of the die, etc. My action plan might require the tooling engineer to fix a specific problem. That's the beauty of speaking with data—we can focus in on a problem and fix it before it causes too much trouble."
As an example, Bossingham describes one of its newer dies, used to form Dodge Ram seat tracks. Initially, the plant experienced trouble running the cam-driven form station on the lower track die, where tolerances are very tight. Looking at the first-piece yield data from the Die Setter Production Report, management learned that tool-makers were constantly tweaking the form station, and the press operator had to adjust shut height to attain 90 degrees. Angles and square walls.
"We eventually redesigned the die based on the reports," says Bossingham, "and discovered that we had insufficient pneumatic lines serving the pneumatic cylinders used to drive the cam forms. We had leaks, insufficient airflow, and sticking. Toolmakers were spending far too much time tweaking that die and not addressing the real problems."
The Bottom Line: Earned Hours or Productivity
Ultimately, the measure of reduced downtime and improved throughput is productivity. Lear measures pressroom productivity with a yardstick it calls earned hours—if, for example, it rates a job at 1600 parts/hr., and successfully produces 1600 parts/ hr., it credits that job for one earned hour. Productivity, therefore, is the ratio of earned hours to hours worked.
A couple of years ago, the Roscommon plant was in trouble regarding its early shift, so the issues don't linger. When they recognize a shortage of earned hours amid a job, managers might send a tooling engineer immediately to troubleshoot a press. Or they might notice that earned hours are down because the press isn't running at the proper stroke rate—maybe an operator slowed the press down due to worries about misfeeds. In that case, management would dispatch a team as soon as possible to find out why the press slowed, and what's needed to get it back up to speed. In the end, the plant has enjoyed a 65-percent jump in pressroom productivity.
"We've made some big, big changes around here in the last year or two," concludes Bossingham, "and a lot of it revolves around the data we now have at our fingertips."