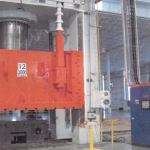
Hydraulics Case Study
October 8, 2024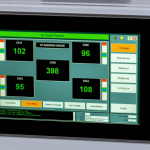
The Importance of Tonnage Monitoring
October 10, 2024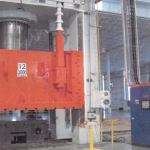
Hydraulics Case Study
October 8, 2024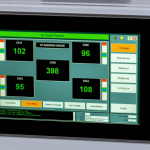
The Importance of Tonnage Monitoring
October 10, 2024For Ernst Metal Technologies, Press-operator efficiency and job satisfaction are top priorities.From aging motors, drives, and other electronic components to new state-of-the-art components, this article from PMA’s MetalForming Magazine is reflective of industry innovations and developments that Toledo has been a part of.
Fifteen years is nothing when it comes to the life of a tamping press and its structural components can last two to three times that long. For drives and controls, 15 years is about the time to breathe new life into the press with an electrical upgrade.
The theme of this story originates from automotive parts manufacturer, ErnstMetal Technologies, and its U.S. facility in Moraine, OH. Established by its German parent company in 2005, the company supplies parts and assemblies primarily for transmissions and thermal management systems throughout North America. Its 100,000 square ft. facility houses six large press lines, including a 2006 vintage 630-ton Mueller Weingarten (MW) transfer press.
Revitalizing a Workhorse:
The MW press has been a workhorse for Ernst since the plant started operations 15 years ago, turning out parts by the millions. From mostly high-strength, low-alloy steel sheets- 0.3 to 6 mm thick.
When press downtime occurred for maintenance purposes, it became more than a nuisance, production management had to act. The Shares Company Vice President and Sales Manager, Tuncay Onur said, "The ongoing issues with the outdated control on this press were impacting overall equipment effectiveness (OEE).
He also shared that, "Lack of available spare electronic components for the press and control system became a significant issue, and we wanted to provide our operators and maintenance team with an updated ed press line that would enable them to be as productive as possible."
The press-refurb project came to a head in November 2020 during a planned six-week window, shutting the press down for maintenance.
Partnering with Toledo Integrated Systems for the turnkey project, Ernst installed a complete control solution for the MW press, as well as its servo transfer system and zig-zag servo feeder. Toledo Integrated, along with a complete press rewire and new electrical enclosures replaced the aging press control with an Allen Bradley GuardLogix Safety PLC. Ohn. Eby, Sales Manager of Toledo shared that this was meant "to run the press, transfer system, and feeder- "We also upgraded two servo axes on the feeder-trans verse and longitudinal-and 12 servo axes on the transfer system, including two for gripper-width adjustment, installing Allen-Bradley Kinetix servo drives."
Included with the project are Ethernet communication to the PLC, safety I/0, HMI, and drives. Also included were updated safety efforts using Allen-Bradley Safety Point I/0 modules, new servo motors, a new Allen-Bradley 275-hp main motor drive, and Toledo Integrated's Press Watch signature-based tonnage monitor, with 1-deg. resolution, and a 19-in. Allen-Bradley PanelView control screen.
"While we don't see many shops go with the large screen," Eby exclaimed, "the advantage can be tremendous. It gives the press operators and the main tenancy team immediate access, on just a few screens, to all of the information they need for setup as well as for production and troubleshooting."
What Makes a Good HMI?
Toledo Integrated manages an entire line upgrade making it easier to ensure that the customer and its various work team production, maintenance, quality, etc. get exactly what they're looking for. In Ernst's case, the custom HMI is exactly what the (press) doctor ordered.
Some of those key HMI characteristics that make it so convenient are:
intuitive and easily understood
Information is conveyed on the home screen based on input from the operators and their individual needs
The large display, so as not to cram too much information onto one screen
HMI graphics that illustrate the production process, to provide better visualization to the operators and maintenance technicians, giving them a sense of the action that's required.
"The home screen includes all of the information the operator needs to know to ensure that the process continues to run per spec," explains Ernst maintenance manager Jacob Crabtree, "that includes press tonnage, feed and press speed, and data on the hydraulic systems." Before the upgrade, the press lubrication system had its independent control station. Now, that functionality is included in the new HMI and at the operator's fingertips.
"From a maintenance perspective," Crabtree continues, "with the original press control troubleshooting, an error message was often complicated and time-consuming. Identifying and locating faults could take hours. This new control pinpoints faults immediately and provides all the information needed to quickly address them. We also can connect a PC to the control to look at the PLC files, greatly streamlining some troubleshooting efforts."
Communication and Data Exchange:
The control also communicates electronically with the Ernst proprietary, in-house-developed machine data acquisition (MDA) system, which sends alerts to plant personnel when a press goes down. "From our phones or computers," explains Crabtree, "we can monitor OEE, and downtime codes as selected by the press operator. The MDA can generate reports, track uptime and downtime, hit rates, etc."
Being that this press takes on mostly long-running jobs and mostly runs eight dies, each for parts with annual production volumes of 800,000 to 900,000-press green-light time is crucial. There's been a remarkable improvement in OEE already, just a few months after the upgrade.
"While it's still very early in the operation of the refurbished press," says Ernst Metal president James Burt, "we're confident, just from an operator and maintenance perspective, that OEE has improved by at least 5 percent. We also know that our operators are much happier on the job and more productive. It's greatly improved operator efficiency and job satisfaction."
Now the Ernst Metal Technologies team has its sights set on another press line control system upgrade, slated for an 800-ton transfer press. "Since we don't have redundancy for that press," Burt adds, "that project will pose more challenges. We'll need to build up an inventory bank. We'll complete that project in two phases-issue the purchase order for the control build and have it ready to go before we take the press out of commission."